CERTIFIED INFRA-RED THERMOGRAPHY AUSTRALIA (CIRTA) PROVIDES THE FOLLOWING SERVICES:
» Electrical System Surveys
» Infrared Testing on High Voltage Equipment
» Building Envelope Performance Surveys (Heat Loss Detection)
» Wall Moisture Surveys
» Residential, commercial, and industrial energy audits
» Mechanical & Equipment Surveys
» Research and Development, Image Acquisition and Post Processing
» Steam / Utilities / Piping Surveys
» Infrared Inspections of Refractory
» Roof Moisture Surveys, Low Slope Roof Evaluation
» Roof Moisture Surveys, Low Slope Roof Evaluation
OUR MISSION
CIRTA’s objective is to cater our valued clients needs in developing maintenance systems that give them vital information that will create safer workplaces while saving their businesses a great deal of time & money.
ELECTRIC FENCING:
We are a True Electric Fencing Specialist & one of the only stores of its kind anywhere in Australia. You can shop with us online 24/7 or deal directly with us at our store, to get all the specialty supplies you need. We stock & Repair all the Best Brands on the market & we provide a full Electric Fencing Design Service to help you setup the best Electric Fencing Systems from the best suppliers & most cost effective solution to suit you individual requirements, with or without Installation or for upgrades & fault finding services to existing fences. (installations service are not available in all areas).
» Electric Fencing Installation
» Electric Fencing Design Servic
» Electric Fencing Repair
» Fault finding services
Why Test Emergency Lighting
Australian Standard AS/NZS 2293.2 1995 relates to inspection and maintenance of Emergency & Evacuation lighting for buildings.
Ensure compliance with Occupational Health and Safety obligations, as employees have a legal ‘Duty of Care’ to ensure that Emergency and Exit Lights work adequately, in a power outage, or other emergency, so people are able to quickly exit their way out of the building.
Emergency lighting is an essential service that is quite often forgotten, until an accident or catastrophe happens in the event the power fails in your building, your emergency and exit lights must remain lit for at least 90 minutes, to allow people safe passage out of the building. It is imperative to maintain all emergency and exit lighting in commercial buildings, to comply with relevant building codes in accordance with Australian Standards (AS/NZS 2293.2).
Not only will you comply with exit testing regulations, but you will have greater peace of mind in knowing that your emergency exit lighting is fully operative.
The Standard instructs that all Emergency evacuation lighting systems shall be inspected and maintained in accordance with the relevant procedures specified in the Standard, and that the inspection and maintenance procedures shall be carried out only by persons having qualifications, and experience suitable for this type of Work.
What are the Testing Intervals?
How is Emergency Lighting Testing carried out?
What legislation applies?
What Compliance Reporting is required?
Who can carry out Inspection & Testing of electrical equipment?
What are the Testing intervals?
Australian Standard AS/NZS 2293.2:1995 states that Exit and Emergency lighting must be tested in accordance to the procedures described in clauses 3.2.2 and 3.2.3, and not exceed intervals of no greater than specified, which is 6 & 12 months.
In accordance with Australian Standards 2293.2 emergency lighting systems are required to be certified periodically, by conducting a 90 minute battery power down (discharge) test.
How is Emergency Lighting Testing carried out?
This test certifies that all the Exit & Emergency lights are functional, and batteries sustain their charge for 90 minutes during a power blackout or building fire.
Six Monthly Tests
Visual checks of all Emergency and Exit lights for mains operation.
Check for operation of maintained exit lights and replace faulty lamps where required.
Where manual discharge test facilities are provided, the following procedure shall be carried out, to check the operation of the emergency lighting system.
Turn the battery charger off, simulate a mains failure and carry out a partial Discharge test at 100 percent of the installed emergency lighting load. Allow the test to continue until the operation of all emergency luminaries, and exit signs has been checked, this test must meet the AS2293 requirement for a duration of 90 minutes.
After tests have been completed the tester must restore the system to normal operation, turn the battery charger on, and recharge the batteries of each fitting.
Where automatic discharge test facilities are provided, a visual check shall be made of the operational status of all emergency luminaries and exit signs, by means of the indications given at the controller or associated indicator panel.
Those units which fail the discharge test must be either repaired and restored to normal condition or replaced.
Where manual discharge test facility is present, operate the test switch and/or circuit breaker to simulate a power failure.
Lamp replacement of any defective lamps shall be replaced, and a match of lamp technology and lamp colour must be used. For emergency luminaries & exit signs with tubular fluorescent lamps, it is recommended that the lamps be replaced if they exhibit excessive end-blackening, even when the lamps still operate
Notes
A check should be made to ensure no interruption to the normal supply has taken place for a period of at least 16h prior to conducting a discharge test
Those units which fail the discharge test must be either repaired and restored to normal condition or replaced.
Twelve Monthly Procedures
Carry out all checks as per six-monthly procedures.
Clean and Inspect fittings and clean reflective surfaces as necessary on all emergency and exit lighting diffusers as required
Visual checks to ensure that the emergency lighting system operates in correct relationship to the normal lighting in any designated area.
What legislation applies?
Australian Standard AS/NZS 2293.2:1995 states that Exit and Emergency lighting must be tested in accordance to the procedures described in clauses 3.2.2 and 3.2.3, and not exceed intervals of no greater than specified, which is 6 & 12 months.
What Compliance Reporting is required?
Report any failures and record data in on site manuals.
Record data in electronic format for OH&S auditing processes.
All maintenance records must be in the form of hard copy record tags or log books.
Electronic copies may also be used.
Any corrective action must also be taken to repair faulty emergency lighting
The names of the persons responsible for carrying out the maintenance work and the date the work was completed
The logbook or alternative record system shall be kept on the premises at all times, or at such other locations as may be approved by the regulatory authority
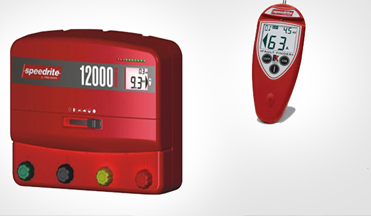
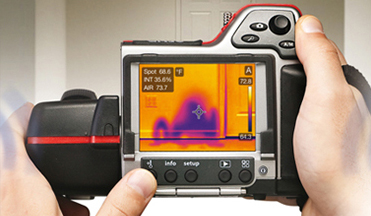
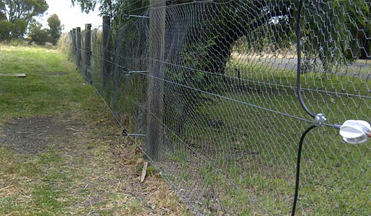
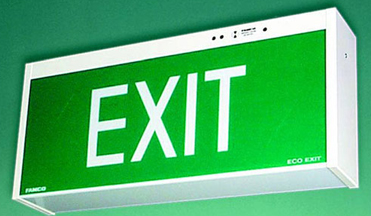
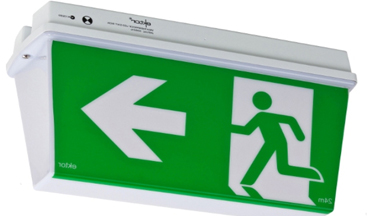